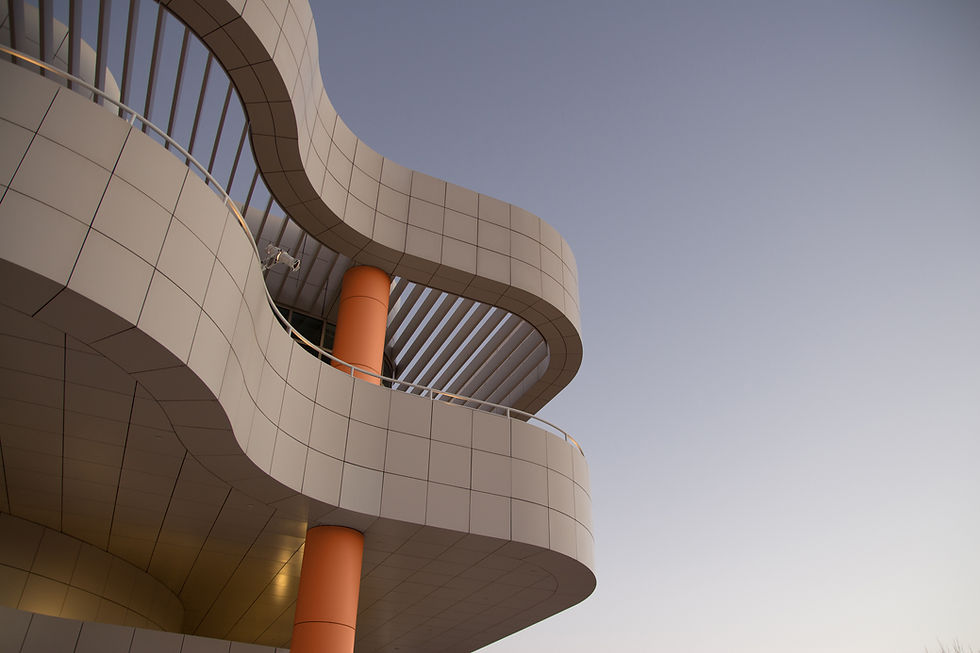
The Essential Guide to Non-Magnetic Tools: Enhancing Safety and Precision in Sensitive Environments
Jul 31, 2024
6 min read
In various industries, the use of non-magnetic tools is crucial for ensuring safety, precision, and efficiency. These specialised tools are designed to eliminate problems where normal steel tooling would create risk. This guide explores the importance of non-magnetic tools, the materials used in their construction, the industries that rely on them, and best practices for their use and maintenance, providing a thorough understanding of why non-magnetic tools are a critical investment for many businesses.
What Are Non-Magnetic Tools?
Non-magnetic tools are hand tools manufactured from materials that do not exhibit magnetic properties. These tools are specifically designed to prevent magnetic interference, making them safe for use in environments where magnetic sensitivity is a concern. Common materials used include brass, bronze, aluminium and titanium.
Key Features of Non-Magnetic Tools
Non-Magnetic Properties: The primary characteristic of these tools is their lack of magnetism, which is crucial for avoiding disruption to sensitive equipment or environments.
Corrosion Resistance: Non-magnetic tools also offer high resistance to corrosion, making them suitable for use in harsh or corrosive environments.
Durability: Despite being non-magnetic, these tools can be highly durable, offering good mechanical strength and wear resistance.
Variety: Non-magnetic tools come in a wide range of types, including wrenches, pliers, screwdrivers, hammers, and more, to suit various applications.
Why Non-Magnetic Tools Are Essential
Non-magnetic tools are vital in environments where magnetic fields can interfere with equipment or processes. For instance, in the medical field, magnetic interference can disrupt sensitive diagnostic equipment like MRI machines. In aerospace, magnetism can affect navigation instruments and avionics. In these contexts, non-magnetic tools ensure that operations are conducted safely and accurately.
Industries That Rely on Non-Magnetic Tools
Medical and Healthcare: Hospitals and medical facilities, especially those with MRI equipment, require non-magnetic tools to prevent interference that could compromise patient safety and diagnostic accuracy.
Aerospace: In the aerospace industry, non-magnetic tools are used to maintain and repair aircraft to avoid interference with sensitive avionics and navigation systems.
Electronics Manufacturing: Manufacturers of electronic devices use non-magnetic tools to prevent damage to delicate components and circuits that can be affected by magnetic fields.
Mining and Explosives: In environments where explosive materials are present, non-magnetic tools are used to avoid the risk of sparks and accidental detonations.
Scientific Research: Laboratories and research facilities, especially those dealing with sensitive measurements or magnetic materials, utilize non-magnetic tools to ensure the integrity of their experiments.
Petrochemical Environments: In petrochemical plants and refineries, non-magnetic tools are essential to prevent sparking and ensure safety in areas where flammable gases and volatile chemicals are present. The absence of magnetic properties reduces the risk of igniting explosive mixtures and enhances the safety of maintenance and repair operations.
Types of Non-Magnetic Tools
Non-magnetic tools are available in various forms, each suited to specific tasks. Some of the most common types include:
Non-Magnetic Screwdrivers: These tools are essential for assembling and disassembling components in sensitive environments. They come in various sizes and tip types, such as flathead and Phillips.
Non-Magnetic Pliers: Used for gripping, bending, and cutting wires, these pliers are crucial in electronics and medical applications where magnetic interference must be avoided.
Non-Magnetic Wrenches: Available in different sizes and styles, non-magnetic wrenches are used for tightening and loosening nuts and bolts without the risk of magnetic interference.
Non-Magnetic Hammers: These are used for tasks that require striking, such as driving nails or fitting components, without creating magnetic fields that could affect sensitive equipment.
Non-Magnetic Sockets and Ratchets: These tools are used in confined spaces where magnetic fields could interfere with operations, such as in electronics assembly or aerospace maintenance.
Materials Used in Non-Magnetic Tools
The effectiveness of non-magnetic tools largely depends on the materials used in their construction. Here are some of the most commonly used materials:
Beryllium Copper:Â This alloy is both non-magnetic and non-sparking, making it ideal for use in explosive atmospheres and around sensitive electronic equipment.
Aluminum Bronze: Aluminum bronze is an alloy known for its excellent corrosion resistance, high strength, and non-magnetic properties. It is widely used in environments where both durability and safety are critical, such as in marine applications, chemical processing plants, and petrochemical industries. The non-sparking nature of aluminum bronze makes it particularly suitable for use in potentially explosive atmospheres.
Titanium: Known for its high strength-to-weight ratio and excellent corrosion resistance, titanium is non-magnetic and suitable for highly demanding environments.
Stainless Steel (Austenitic Grades): Certain grades of stainless steel, particularly austenitic types like 304 and 316, are non-magnetic and are used in environments requiring corrosion resistance and durability.
Compliance and Standards for Non-Magnetic Tools
While there are no universal standards specific to non-magnetic tools, many industries adhere to strict guidelines to ensure that tools do not interfere with sensitive equipment. For example:
ASTM F2063: This standard covers the requirements for tools used in the presence of magnetic resonance imaging (MRI) systems, specifying non-magnetic properties to avoid interference.
ISO 6020: Pertains to non-magnetic tool testing for use in explosive atmospheres, ensuring that tools do not generate sparks or magnetic fields.
ATEX Directive (2014/34/EU): The ATEX directive specifies the requirements for equipment and protective systems intended for use in potentially explosive atmospheres. It includes standards for testing and certifying tools to ensure they do not act as ignition sources in explosive environments. Compliance with ATEX is essential for tools used in European markets, particularly in industries like oil and gas, chemical processing, and mining.
Companies must verify that their non-magnetic tools meet relevant standards and specifications, particularly in industries like healthcare and aerospace where the consequences of magnetic interference can be severe.
Our Product Range: Explore our extensive selection of non-magnetic tools tailored for various industries here.
Best Practices for Using Non-Magnetic Tools
To ensure the effectiveness and longevity of non-magnetic tools, it’s important to follow best practices:
Regular Inspection: Always inspect non-magnetic tools for any signs of wear or damage before use. Damaged tools may lose their non-magnetic properties and should be replaced immediately.
Proper Use: Use non-magnetic tools only for their intended purposes. Using these tools inappropriately can cause damage to the tools and compromise their non-magnetic qualities.
Storage: Store non-magnetic tools in a dry, controlled environment to prevent corrosion and maintain their non-magnetic properties.
Cleanliness: Keep tools clean and free from contaminants that could introduce magnetic materials or interfere with their performance.
Certification Verification: Ensure that tools meet industry standards and specifications, especially when used in critical applications like medical or aerospace settings.
Maintenance and Care of Non-Magnetic Tools
Maintaining non-magnetic tools involves regular cleaning and inspection. Here are some key maintenance practices:
Cleaning: After use, clean tools with mild detergents and water to remove any debris or contaminants. Avoid abrasive cleaners that could damage the tool’s surface or alter its properties.
Inspection: Regularly inspect tools for signs of wear, such as scratches or dents, which could compromise their non-magnetic properties. Tools should also be tested periodically for any magnetic characteristics.
Storage: Store tools in a dry, cool place, away from other metal objects that could impart magnetic properties. Use protective cases or toolboxes to prevent damage.
Replacement: Replace tools that show signs of wear or damage, as they may no longer provide the necessary level of safety and performance.
Investing in Non-Magnetic Tools: A Strategic Choice
Non-magnetic tools are a crucial investment for industries where magnetic interference poses a significant risk. Although these tools may come at a premium compared to standard tools, their benefits far outweigh the costs. Non-magnetic tools help prevent costly equipment damage, ensure safety in sensitive environments, and maintain the integrity of operations.
How to Purchase Non-Magnetic Tools
When purchasing non-magnetic tools, it’s important to select products from reputable manufacturers known for quality and reliability. Look for certifications and compliance with industry standards. Consider the specific needs of your application, including the type of work being performed and the environment in which the tools will be used.
Conclusion
Non-magnetic tools play a critical role in ensuring safety and precision in industries where magnetic fields can interfere with equipment or processes. From healthcare and aerospace to electronics manufacturing and scientific research, these tools are indispensable for maintaining operational integrity and safety. By investing in high-quality, certified non-magnetic tools and adhering to best practices for their use and maintenance, companies can protect their workers, equipment, and the integrity of their work.
For more information on non-magnetic tools and to explore our comprehensive range of products, visit our product pages and learn more about our commitment to providing the best in safety and precision tools.
Whether you're in the medical field, aerospace industry, or any other sector where magnetic interference is a concern, we have the non-magnetic tools you need to perform your work safely and effectively. Contact us today to learn more and find the right tools for your specific needs.